
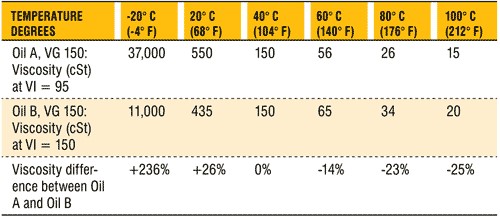
- #Viscosity index verse viscosity number manual#
- #Viscosity index verse viscosity number Pc#
- #Viscosity index verse viscosity number plus#
The reason they called for a straight 40 weight was that, at the time, it would offer the best protection in a hotter running air-cooled engine on hot days and high engine loads. Some makers publish HTHSV, and some you have to email and ask.

It is a good measure of the overall film strength of the oil at high temperatures. The HTHS viscosity is the primary factor in wear protection that has any relation to viscosity. Generally speaking, you want an oil with the lowest grade numbers you can get away with, and the highest HTHS (high temperature, high sheer) viscosity number. I'm just going to throw out a general fact that few people understand about motor oil and let it get ignored and buried in the inevitable same-old-discussion, but at least I'll put it out there. In the winter I run 0W30 since I deal with temperatures in the single digits sometimes. If you stop and then start it will be a lot warmer for a period of time causing oil temperatures to climb for a while.

#Viscosity index verse viscosity number plus#
Plus I have a thermometer in my engine compartment and it is usually 10 degrees warmer in the engine compartment than ambient temperature. Also if you run 200f oil temps at 70f at 90 it will be closer to 220f and less viscosity hence lower oil pressure. I do not think running a thinner oil will run any cooler than a thicker oil in the summer, they should all flow through the oil cooler when hot and cool the same. But it seems unrealistic to switch to 40w for a few weeks and with weather where it gets below 70f and then peaks at 95+f what is one supposed to do? I found 25w60 oil exists and have thought maybe that would be more applicable if you are constantly encountering peak temperatures above 85f.
#Viscosity index verse viscosity number manual#
If I knew I would be in temperatures above 70f all the time in the summer I would go ahead and run 40w like the manual says. temp.html In the 1985 vanagon manual it has the same oil weight guidelines as the 1982 aircooled manual: 20-50 (or other multi 50w oil) up to 85f and temperatures above that use 40w. I think the upper limit was about 85 degrees Fahrenheit. When you factor in the variations in the amount of melt at any point, and gain or loss from barrel heating/cooling, it makes for a complicated analysis even with very sophisticated computer simulation.The operating instructions for the industrial engines listed a range of air temperatures at which you could run with a maximum load on the engine. In addition, polymers all vary considerably in specific heat, density, crystallinity and thermal conductivity. The calculations to reach the proper melt temperature for each polymer are relatively complicated and require a desired melt temperature as a target, which can vary with every extrusion process. That is why just looking at some shear-rate/viscosity curves does not provide enough information to design a screw. HDPE and PP are not normally processed in a dried state.
#Viscosity index verse viscosity number Pc#
Nylon 66 and PC are both typically processed after drying, with consequent heating, thereby reducing the required energy and viscous dissipation. PC is in a different range than nylon 66 due to its very high power-law coefficient. Nylon 66 is totally different and would need a much higher shear rate to match the viscous dissipation of the HDPE. Just looking at some shear-rate/viscosity curves does not provide enough information to design a screw.
